Hydraulic Power Unit Working Principle
Release time: 2025-04-12
The hydraulic power unit is the core component of a hydraulic system. Its main function is to provide power and fluid control for the hydraulic system, ensuring the system operates efficiently under the required pressure. The hydraulic power unit converts mechanical energy into hydraulic energy through the coordination of hydraulic oil pumps and axial-flow pumps, and delivers this energy to hydraulic actuators, thus controlling the movement of mechanical equipment. This article will explain the overall working mechanism of the hydraulic power unit, starting from the working principles of hydraulic oil pumps and axial-flow pumps.
Working Principle of Hydraulic Oil Pump
The hydraulic oil pump is a crucial part of the hydraulic power unit, and its main function is to provide flow and pressure to ensure the normal operation of the hydraulic system. The hydraulic oil pump converts mechanical energy into hydraulic energy by drawing in fluid and pressurizing it.
Hydraulic oil pumps can be classified into gear pumps, vane pumps, and piston pumps based on their working principles and structure. Although each type of pump works differently, they all follow the same basic principle—by changing the pump’s internal volume, the fluid is forced to flow and pressurize.
- Gear Pump: The gear pump is one of the most common types of hydraulic oil pumps. It works by using meshing gears to draw liquid into the pump body and then pushing it out. During the rotation of the gears, the relative motion between the gears creates a sealed oil chamber, causing the liquid to be pressurized and output. The hydraulic oil is pressurized due to the engagement and gaps between the gears, ensuring the hydraulic system’s pressure output.
- Piston Pump: A piston pump uses the reciprocating motion of pistons inside the pump body to change the volume, driving the liquid flow. The relative motion between the pistons and the pump body precisely controls each oil intake and discharge, making piston pumps ideal for high-pressure, high-flow hydraulic systems.
Regardless of the type, hydraulic oil pumps ensure the continuous operation of the hydraulic system by drawing in oil, pressurizing it, and discharging it.
Working Principle of Hydraulic Axial-Flow Pump
The hydraulic axial-flow pump is different from traditional hydraulic pumps and is typically used in hydraulic systems that require high flow and low pressure. Its primary function is to push the fluid along the pump’s axial direction.
The structure of the hydraulic axial-flow pump is relatively simple, typically including a rotor, blades, pump body, and outlet. When working, fluid is drawn into the pump body from one end, and the rotor’s rotation drives the fluid to flow along the axial direction, sending it to various components of the hydraulic system. The key feature of the hydraulic axial-flow pump is that the fluid flows along the pump’s axis, not radially, allowing it to deliver continuous, stable high flow output.
Unlike other hydraulic pumps, the flow rate and pressure of the hydraulic axial-flow pump depend on the rotor speed and blade design. The angle and speed of the blades during rotation affect the fluid’s flow speed and pressure, thus influencing the operation of the hydraulic system. The hydraulic axial-flow pump’s advantages include simple structure, high flow, and adaptability, making it ideal for applications requiring large-scale fluid transport, such as in ships and construction machinery.
Overall Working Principle of Hydraulic Power Unit
The hydraulic power unit works by the close cooperation of the hydraulic oil pump and hydraulic axial-flow pump, converting mechanical energy into hydraulic energy and delivering it through the hydraulic fluid to drive various components of the hydraulic system. The main working process of the hydraulic power unit can be broken down into several stages:
- Energy Conversion and Pressure Generation: The hydraulic oil pump converts mechanical energy into hydraulic energy and pressurizes the oil, which is then pumped into the hydraulic system. During this process, the hydraulic oil pump provides the required flow and pressure, enabling the hydraulic system to function.
- Fluid Transport and Load Actuation: The hydraulic axial-flow pump drives the fluid along the axial direction through the rotation of the rotor, ensuring that the fluid is stably delivered to the various actuators in the hydraulic system. The high flow output of the hydraulic axial-flow pump meets the demands of equipment requiring continuous, stable flow, especially in systems where such demands are crucial.
- System Control and Regulation: Pressure and flow control valves, pressure sensors, and flow controllers in the hydraulic system regulate the flow and pressure of the pump output based on actual operational requirements. These control devices allow for precise control over the speed and force of hydraulic equipment, enabling accurate operation of mechanical devices.
- Power Output and Actuation: The hydraulic power unit delivers the pressurized hydraulic oil to the hydraulic actuators through pipelines. The actuators convert the pressure and flow of the fluid into mechanical motion, driving the mechanical equipment. Hydraulic actuators may produce either linear motion (such as hydraulic cylinders) or rotary motion (such as hydraulic motors), depending on the design requirements of the hydraulic system.
Applications and Optimization of Hydraulic Power Unit
Hydraulic power units are widely used in fields such as construction machinery, ships, aerospace, and mining equipment. The design of the hydraulic system and the selection of the hydraulic power unit are crucial for different working conditions and requirements. To ensure the efficient operation of the hydraulic power unit, it is important to choose the appropriate oil pump, axial-flow pump, and related control components based on the system’s specific needs.
Additionally, the maintenance and upkeep of hydraulic systems are equally important. The cleanliness of hydraulic oil, the lubrication of the oil pump and axial-flow pump, and the stability of the system’s pressure all affect the performance of the hydraulic power unit. Therefore, regularly checking and replacing hydraulic oil, cleaning impurities from inside the oil pump, and maintaining the sealing of the hydraulic system are key measures to ensure the long-term stable operation of the hydraulic power unit.
In conclusion, the hydraulic power unit ensures the high efficiency and reliability of hydraulic systems in various industrial applications through its precise working principle and high degree of cooperation. With proper design and optimization, the hydraulic power unit not only enhances the efficiency of equipment but also ensures high and stable performance under complex operating conditions.
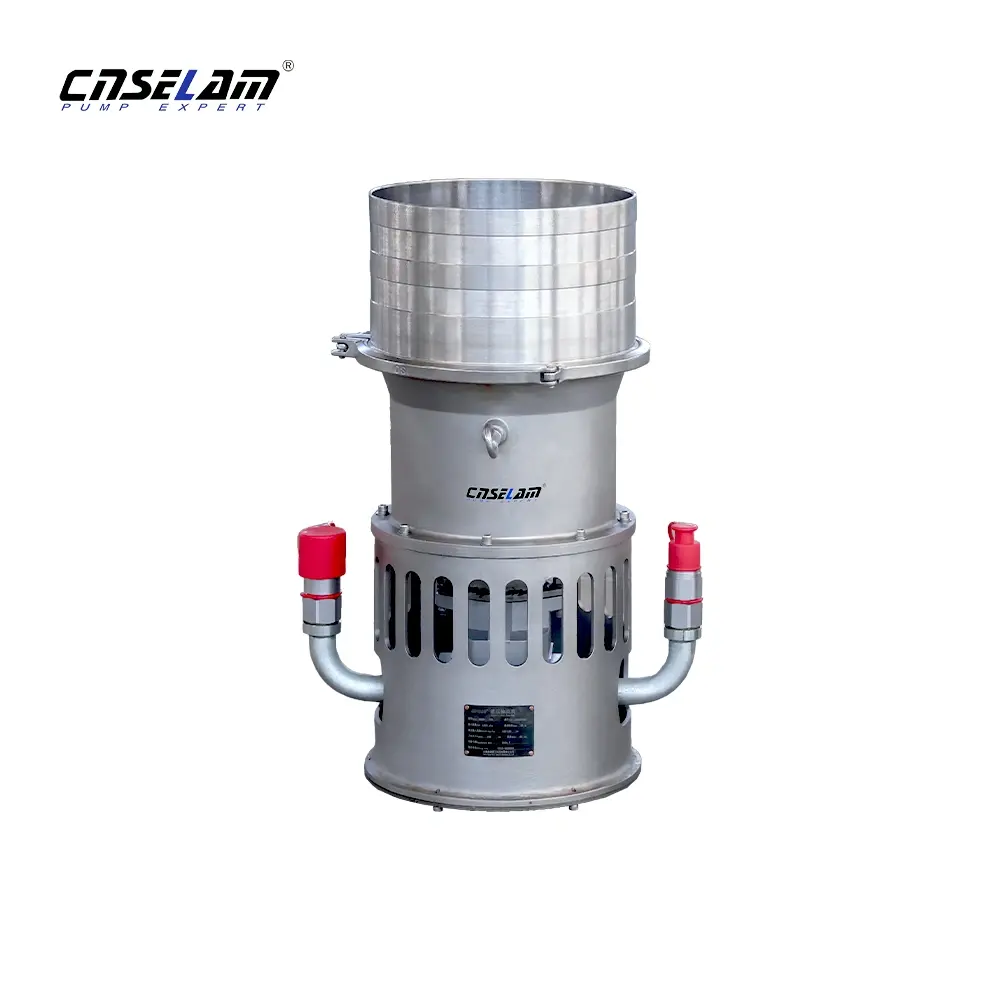
